
Frequently Asked Questions Can I use motor oil in my air compressor? Usually, it is recommended that you change oil after every 1000-2000 hours of runtime. Check your manufacturer’s recommendations before purchasing new oil. Remember that oils vary depending on their viscosity.
Compressor oil professional#
If you suspect that your oil is degrading faster than it should due to contamination, a professional will perform the IR or TAN test to confirm this. If these methods do not give you a clear answer, use other methods such as the blotter test. To check oil quality, use the dipstick or sight glass methods. If your oil is thick and opaque, has grainy particles, and smells bad, then its quality has degraded. Old and worn-out oil could affect the efficiency of your air compressor. #3 Check oil qualityĪs oil gets used in the compressor chamber, it gets old and worn out. Note that if you constantly have to keep refilling your oil pan, the compressor might be leaking an excessive amount of oil. Check regularly for leaks by watching for pooling of oil at the base of the compressor and engine. #2 Check for oil leaksĪn undetected oil leak will leave your oil pan empty, putting your engine at the risk of damage.
Compressor oil full#
The trick is to make sure that the oil level is 2/3 full on the sight glass. Compressors have either a dipstick or a sight glass that you can use to check the oil level.Īll dipsticks are calibrated, and you should make sure that your oil level is always near the max mark. Inspect your oil level 3-4 times a week to make sure that your compressor does not run low on oil. If you have not been monitoring your compressor oil, you can begin doing so using the following tips: #1 Check oil level You should check your lubricant for contamination, which could affect the acidity and viscosity of the liquid. Knowing how important oil is to the smooth running and longevity of a compressor, it makes sense to monitor it. Monitoring air compressor oil will lower costs by: Since a number of moving parts such a bearings help in compressing air, it is important to keep them lubricated. Oil prevents wear and corrosionĪs we mentioned at the beginning of the article, lubrication is one of the functions of air compressor oil. If heat is not rapidly removed from the chamber, bearings, seals, and gears will fail. Oil acts as a primary coolant, keeping the compressor cool.
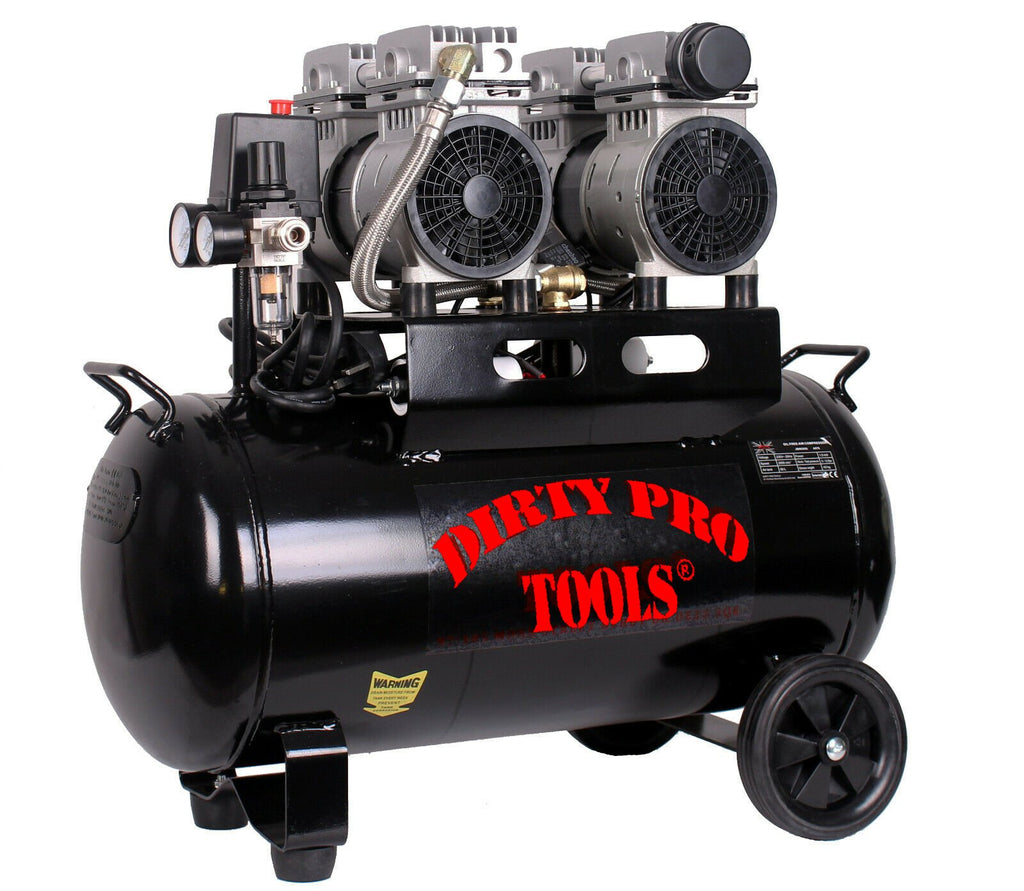

Since air compression is a continuous process that generates lots of heat, temperatures in the compression chamber tend to rise. Consequently, the sealing by oil prevents air from escaping and keeps it compressed. Oil is good at reaching the smallest positions, which ensures that the system is totally sealed. The screws that join metal parts can sometimes make air compression hard because they leave gaps in the machine. Oil helps in the compression process by sealing gaps between screw elements. In turn, this enables the compressor to function efficiently. The particles can then be removed every time you change your oil. Oil captures these nanoparticles and all other particles that are produced by the metal parts of the compressor. They can also be in the form of dust from air molecules being squeezed together.
Compressor oil free#
These nanoparticles can be in the form of free water from water vapor in the air. However, some nanoparticles, which are hard to capture, are still found in the air. Oil acts as a cleaning agentĪir filters are designed to catch most contaminants and particles before they get into the compressor. When using a lubricated air compressor, it’s important to check your oil because: 1. 4 Conclusion The Importance of Monitoring Air Compressor Oil
